広島県では、県が主導して、AI/IoT、ビッグデータ等の最新のテクノロジーを活用して、様々な産業・地域課題の解決のために、複数の事業者が共創しながら解決に向けての試行錯誤ができるオープンな実証実験の場として「ひろしまサンドボックス」を構築している。2018年から実証実験を行う事業者を募集し、3年間でおよそ10億円の投資を行う予定となっており、今まさにその取り組みが”検証フェーズ”にある。
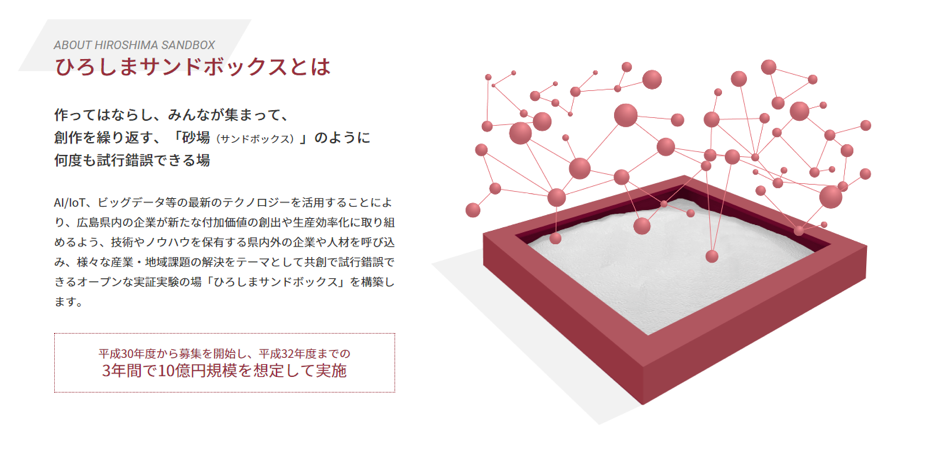
今回はその取組の中の一つである、「つながる中小製造業でスマートものづくり」の実証事業について取材させていただいた。今回の実証事業の主幹はデジタルソリューション株式会社という広島県にあるIT系の会社だ。デジタルソリューション社の事業は主にものづくり企業に向けたITサービスの提供だ。そのサービスを提供する中で、「金属の切削加工」を行う加工プロセスは属人性が高く、中小製造業は人手不足に悩んでいることを目の当たりにし、今回の実証事業の着手に至ったという。
今回デジタルソリューション社が着目したのは、切削加工の中でも”試作”を主に手がける企業の加工プロセスだ。”試作”製作には、短納期要求や仕様変更や数量変更要求が多い。加工計画は流動的で週や月単位での”計画”は意味を成さない。毎日毎日その日の朝にその日の分だけの加工計画を作って運用することを繰り返すことになる。こうなると、日々の計画を作るスキルは属人化していき、その加工計画が最適なのかすら誰もわからない状況になってしまう。加工プロセスの途中に顧客による確認が入るケースもあり、工作機械が稼働していないアイドリングタイムが発生することも多々ある。
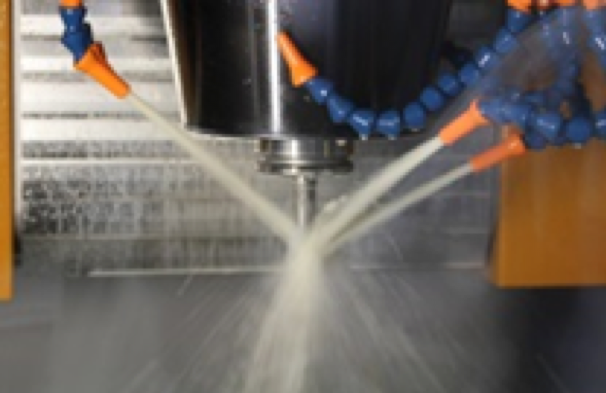
このような「加工計画の最適化」「設備の稼働していないアイドリングタイム」といった課題を解決すべく、今回の実証事業は進んでいる。検証のステップとしては以下の通りだ。
・加工ラインにIoTを導入し設備の稼働状況を可視化
・加工計画の立案や再編をIT化
・加工計画と設備の稼働状況の情報を統合して最適化シミュレーションを実施
・生産設備のアイドリングタイムの可視化と複数事業者間での情報シェア
・シェアされた情報を統合した設備のシェアリングサービスなどの展開の検討
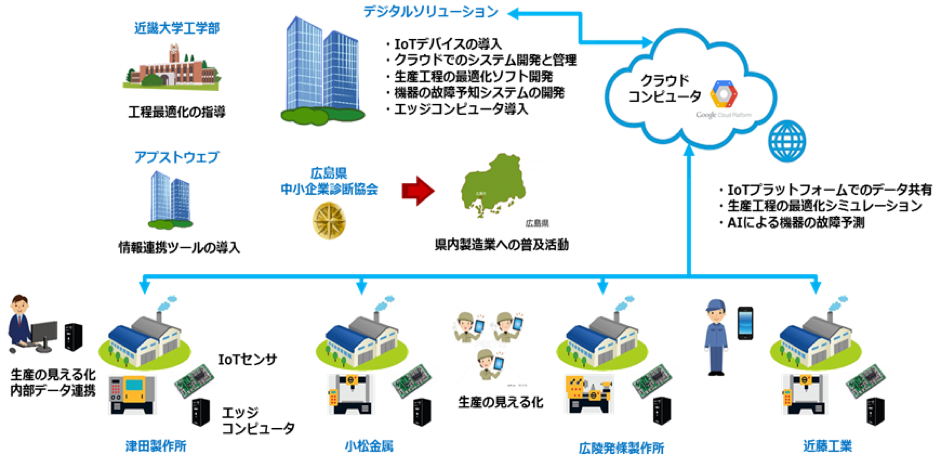
最終的には加工ラインの生産性向上のためのサービスとして提供することを目標としている。現在(2019年5月時点)は、加工ラインへのIoT実装によるデータ取得とそのデータの統合を行う検証を行っている。
取り組んでいる検証は大きく分けると
1:工具や測定具の貸出状況をIoTによって可視化する
2:工作機械の稼働状況をパトランプ点灯や水位センサによって可視化する
の2つである。それぞれについて、以下で解説する。
1:工具や測定具の貸出状況をIoTによって可視化する
工具や測定具は複数の加工ラインで共有されることが多く、特定の加工プロセスで「使いたいときに無い」「探すのに時間がかかる」ということが度々発生していた。これをIoTによって可視化できるようにすることで、工具や測定具を探す時間を無くし、加工時間を短縮することができる。更に加工計画に合わせて、工具や測定具を最適な箇所に配置することも可能になるだろう。
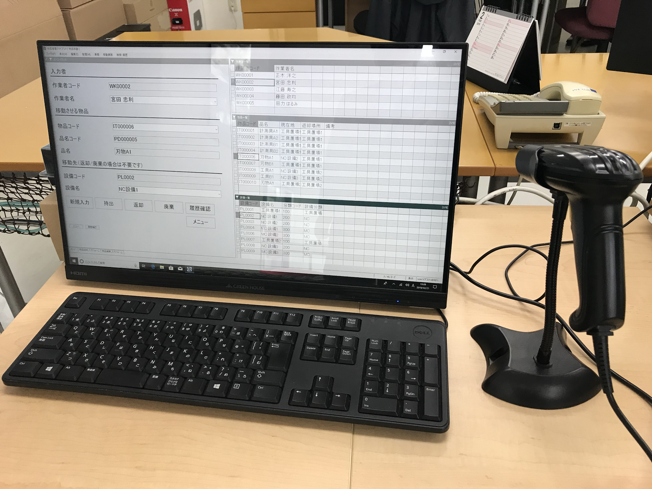
2:工作機械の稼働状況をパトランプや水位センサによって可視化する
工作機械が現時点でどのような状況なのか、あるいは計画に対してどの案件でどれくらい稼働したのかといったデータは今まで取得されてこなかった。急な納期変更や数量変更があった場合、工場に行って工作機械の稼働状況を目視して見なければいけないという工数もかかる上、計画に対して実績の工数や納期がどうだったのかを管理していかなければ利益を上げるための見積もり精度も上がらない。今回の検証は、既存の工作機械のパトランプや冷却水槽にそれぞれ照度センサーと水位センサーを設置してデータを取得できるようにしている。
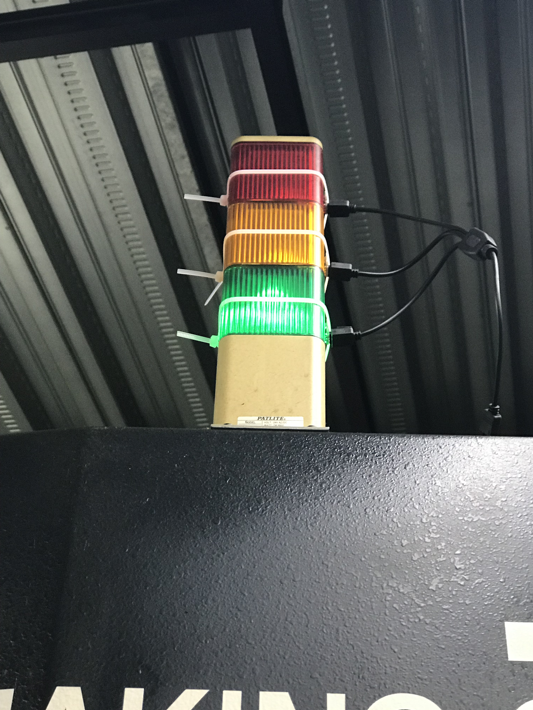
2020年3月までにはこれらのデータ収集を複数社に展開して幅広く行い、工作機械の稼働状況を事業者間でシェアし、設備の有効活用とシェアリングサービスへと発展させる予定だ。これらで取得されるデータと加工計画が統合され、最適な加工計画を導き出すためのアルゴリズムの検証は近畿大学と共同して行っていく予定だ。
前段でも述べたが、この事業の着目すべきポイントは「事業社間のIoTデータのシェア」にある。データをもとにしたシミュレーションやアルゴリズムの精度向上のためにはデータの分母が大きいことが重要であるため、中小企業単独で取り組むには限界があった。今回の取り組みはその限界を中小企業間でのデータをシェアすることで解決しようとする意欲的な試みである。更に、データだけではなく、システムもクラウドで必然的にシェアされるため中小企業にとってはシステム導入の負担も単独での取り組みよりも相対的に下がることが期待される。